The role of IoT in transforming manufacturing processes
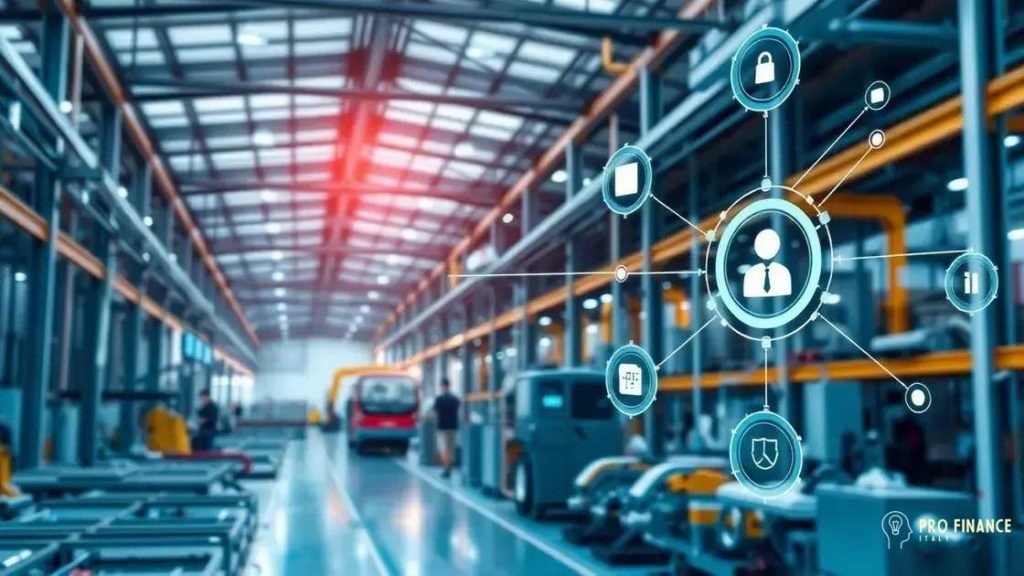
The role of IoT in transforming manufacturing processes includes real-time data monitoring, predictive maintenance, and enhanced efficiency, paving the way for increased automation and reduced operational costs.
The role of IoT in transforming manufacturing processes is more significant than ever, as companies look for ways to increase efficiency and minimize costs. Have you ever wondered how smart devices can revolutionize a factory’s operations? Let’s dive into this exciting topic.
Understanding IoT and its impact on manufacturing
Understanding IoT and its impact on manufacturing is essential for modern industries. The Internet of Things connects devices, allowing them to communicate and exchange data. This leads to increased efficiency, better decision-making, and enhanced productivity.
In manufacturing, IoT plays a vital role in streamlining processes. Companies can monitor equipment and gather real-time data, which helps them respond to issues before they escalate. For example, factories equipped with sensors can detect when machinery is likely to fail, enabling proactive maintenance.
Key Advantages of IoT in Manufacturing
Integrating IoT offers many benefits, including:
- Enhanced operational efficiency
- Improved supply chain management
- Data-driven decision making
- Cost savings through timely maintenance
These features empower manufacturers to optimize their operations significantly. Furthermore, the data collected can lead to innovations in production processes. With IoT, manufacturers can analyze trends that reveal new opportunities for growth.
Challenges in IoT Adoption
Despite its benefits, there are challenges in implementing IoT technologies. Manufacturers may face:
- High initial investment costs
- Integrating with existing systems
- Ensuring data security and privacy
Addressing these challenges is critical for successful adoption. As technology evolves, solutions are emerging, making it easier for manufacturers to leverage IoT functionalities.
Overall, understanding the role of IoT in manufacturing drives innovation. By recognizing its impact, companies can better prepare for the future and stay ahead in a competitive environment.
Key benefits of IoT integration in factories
Integrating IoT in factories presents numerous benefits that can significantly enhance operations. By adopting IoT technology, manufacturers can streamline their processes, improve productivity, and reduce costs.
One major advantage is real-time monitoring of machinery and equipment. This allows for constant oversight, enabling quick responses to potential issues. With sensors placed throughout the production line, workers can receive alerts if something is amiss. As a result, manufacturers can minimize downtime and maintain efficiency.
Enhanced Operational Efficiency
Another benefit of IoT integration is enhanced operational efficiency. By collecting data from various devices, companies can optimize their workflows. This data analysis helps identify bottlenecks in production and highlights areas that need improvement.
- Automated data collection reduces human error.
- Improved coordination between departments.
- Greater flexibility in production schedules.
The IoT also enables predictive maintenance. This proactive approach helps prevent equipment failures. With predictive analytics, factories can determine the best times for maintenance, reducing unplanned downtime and extending the lifespan of machinery.
Cost Savings
Cost savings are another critical aspect of integrating IoT. By reducing downtime and improving efficiency, companies can lower operational costs. Furthermore, IoT allows for better inventory management. Having real-time data means factories can keep optimal stock levels, preventing excess inventory and minimizing waste.
In essence, the benefits of IoT integration in factories are clear. With real-time insights, enhanced efficiency, and significant cost reductions, manufacturers can position themselves for success in a competitive landscape.
Real-world examples of IoT in manufacturing
Real-world examples of IoT in manufacturing showcase the transformative power of this technology. Companies across various industries are adopting IoT solutions to optimize their operations and stay competitive.
One notable example is General Electric (GE), which uses IoT to monitor the performance of its jet engines. By collecting data from sensors embedded in their engines, GE can predict when maintenance is needed, preventing costly downtime and ensuring safety.
Siemens and Smart Factories
Siemens has also embraced IoT through its Smart Factory initiative. In their facilities, they utilize connected devices to automate production lines. This integration allows for greater efficiency and reduced production times.
- Data from machines helps improve operational workflows.
- Workers receive real-time alerts for maintenance and quality control.
- Remote monitoring allows for centralized management from anywhere.
Companies utilize IoT for supply chain management. Amazon, for instance, employs IoT devices in its warehouses. This technology tracks inventory levels in real-time, ensuring that products are readily available, which accelerates order fulfillment.
Procter & Gamble Innovations
Procter & Gamble (P&G) has implemented IoT to monitor production quality. They use sensors to gather data on product consistency during manufacturing. This proactive approach helps them deliver high-quality products to consumers.
From monitoring equipment health to enhancing supply chain efficiency, real-world applications of IoT in manufacturing illustrate its incredible potential. These examples show how different industries leverage IoT to improve processes and drive success.
Challenges faced in IoT adoption
Challenges faced in IoT adoption can impact the effectiveness of this technology in manufacturing. While the benefits are significant, many companies encounter obstacles that can slow down implementation.
One major challenge is the high initial cost associated with deploying IoT solutions. Investments in new hardware, software, and infrastructure can be substantial, creating hesitance among businesses, especially smaller ones, that may not have the required budget.
Integration with Legacy Systems
Another significant barrier is integrating IoT with existing legacy systems. Many factories rely on older machines that may not be compatible with new technology. This disconnect can lead to inefficiencies and additional costs as companies attempt to bridge the gap.
- Data silos can form if systems are not compatible.
- Upgrades or replacements may be necessary, adding to expenses.
- Training staff to work with new systems can take time and resources.
Moreover, data security and privacy concerns are prevalent in the IoT landscape. The more connected devices there are, the greater the risk of cyberattacks. Manufacturers need to invest in robust security measures to protect sensitive information and ensure compliance with regulations.
Change Management
Finally, change management within organizations can be a hurdle. Employees may resist the transition to IoT technologies due to fear of job loss or changes in their roles. Engaging and training staff on the advantages of IoT is essential to foster acceptance and ensure a smooth transition.
Addressing these challenges is crucial for companies eager to adopt IoT technologies. By understanding the barriers and planning appropriately, businesses can set themselves up for success as they embrace the IoT revolution.
Future trends of IoT in the manufacturing sector
Future trends of IoT in the manufacturing sector promise exciting advancements that will transform industries. As technology continues to evolve, manufacturers are looking toward new innovations that enhance efficiency and productivity.
One anticipated trend is the rise of edge computing. This technology allows data processing to occur closer to the source of data generation, enabling quicker decision-making. With edge computing, factories can analyze production data in real time, reducing latency and improving response times.
Increased Automation
Another significant trend is the push towards increased automation. As IoT continues to develop, robots and automated systems will be more integrated into manufacturing processes. This automation will not only enhance efficiency but also reduce the need for manual labor in dangerous environments.
- Robotic arms for precise assembly tasks.
- Automated guided vehicles for material transport.
- Smart quality control systems using sensors.
Predictive maintenance will see even greater adoption in the future. With advancements in machine learning and data analytics, manufacturers will be able to predict equipment failures more accurately. This proactive approach will save time and reduce maintenance costs, leading to more streamlined operations.
Enhanced Connectivity
Enhanced connectivity among devices is also on the horizon. The next generation of wireless technology, such as 5G, will provide the bandwidth necessary for more devices to connect simultaneously. This increased connectivity will support a more integrated manufacturing environment, allowing for seamless communication between machines.
Lastly, as data privacy concerns grow, manufacturers will need to adopt stronger security measures. The future of IoT in manufacturing includes developing more robust cybersecurity protocols to protect sensitive information from cyber threats. Overall, the future trends in IoT hold great promise for the manufacturing sector, paving the way for more efficient, automated, and secure production processes.
IoT in the manufacturing sector brings about transformative changes. Companies benefit from real-time monitoring, improved efficiency, and data-driven decision-making. However, challenges like high costs and security concerns remain. Looking towards the future, we can anticipate advancements that will further enhance automation and connectivity. Embracing these trends will be crucial for manufacturers aiming to thrive in a dynamic landscape.
FAQ – Frequently Asked Questions about IoT in Manufacturing
What are the main benefits of implementing IoT in manufacturing?
The main benefits include real-time data monitoring, improved efficiency, reduced maintenance costs, and enhanced decision-making.
What challenges do companies face when adopting IoT technologies?
Companies often face high initial costs, integration issues with legacy systems, security concerns, and change management difficulties.
How does predictive maintenance work with IoT?
Predictive maintenance uses data from IoT devices to predict equipment failures before they occur, allowing for timely maintenance that minimizes downtime.
What future trends can we expect for IoT in manufacturing?
Future trends include increased automation, enhanced connectivity through technologies like 5G, and more robust cybersecurity measures.